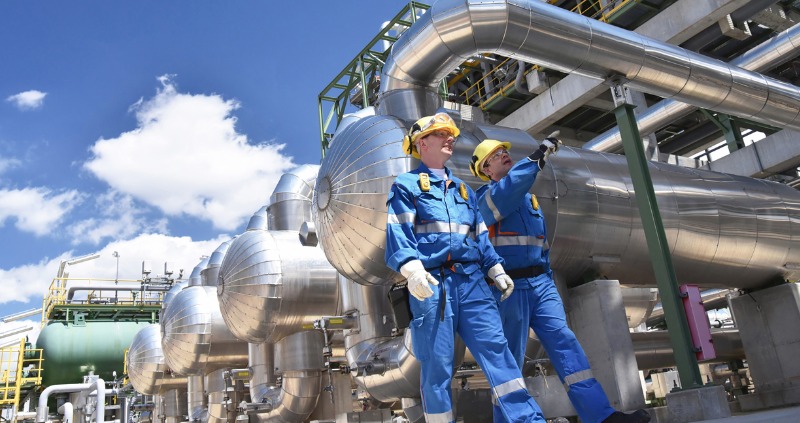
Electrical equipment including rugged devices are sold with certifications so they’re instantly recognisable as being safe in hazardous environments. The two certifications ATEX and IECEx are similar but there are important differences that rugged device users should be aware of.
What is Ex Equipment?
Ex equipment is needed in locations that have potentially explosive atmospheres.
An explosive atmosphere has air, an ignition source and at least one of three substances present - flammable gas, vapour, mists and combustible dusts present.
Equipment can be the ignition source if its electrical circuits can raise the temperature on the surface, inside the equipment or if the electrical device generates arcs or sparks. The equipment can range from large processing or manufacturing equipment to small, handheld devices such as a rugged tablet. The equipment’s size and function doesn’t matter if it has the potential to ignite an explosive atmosphere.
Ex equipment is required in a range of industries including:
- Oil and gas rigs, petrochemical refineries and processing plants
- Oil and gas tankers, drilling ships and offloading vessels
- Petrol and refuelling stations
- Printing industries
- Aircraft refuelling and hangars
- Hospital operating theatres
- Painting and coating operations
- Coal mines
- Sewerage treatment plants
- Gas and petrol pipelines
- Grain handling and storage
- Woodworking
- Sugar refineries
- Light metal working
- Hydrogen technology
Categories of Hazardous Area Zones
Sites are categorised according to the presence and frequency of explosive materials in certain areas. A zone determines which category of equipment is required. The most explosive atmospheres are classified as Zone 0 because explosive mixes are always present. Sites classified as Zone 2 infrequently have explosive mixes.
Gas/Vapour/Mist Environments
- Zone 0 – Explosive mixtures are present continuously. Category 1 equipment required.
- Zone 1 – Explosive mixtures are present intermittently. Category 2 or 1 equipment required.
- Zone 2 – Explosive mixtures are present abnormally or infrequently. Category 3, 2, or 1 equipment required.
Dust/Fibre Environments
- Zone 20 – Hazardous material is present continuously, for long periods, or frequently.
- Zone 21 – Hazardous material is likely to occur in normal operation occasionally.
- Zone 22 – Hazardous material is not likely to occur in normal operation but, if it does occur, will persist for a short period only.
Certifying Ex Equipment
Equipment that can cause ignition in an explosive environment must be made safe to ensure there is no heat, arcs or sparks. An explosion or fire on a site can cause workers to suffer catastrophic injuries or death. The site can be destroyed and cause environmental damage.
Organisations have an obligation to ensure only safe equipment is taken into potentially dangerous locations. Industry standard certifications ensure all equipment passes the same set of requirements. There are two main certifications used in the world to certify equipment as safe - ATEX and IECEx.
ATEX Certification
ATEX comes from the French words ATmosphere EXplosibles. Electrical equipment and protective systems require ATEX certification for protection against workplace hazards in the European Union. Manufacturers label equipment as ATEX certified so it can be purchased by organisations working in the EU.
Certified products bear the yellow and black Ex badge so it's instantly recognisable as being safe. ATEX certification isn’t recognised in Australia.
IECEx Certification
IECEx stands for International Electrotechnical Commission Explosive. IECEx is a global certification standard that provides a framework for regulating hazardous workplace atmospheres. IECEx reduces trade barriers caused by different conformity assessment criteria across different countries.
IECEx certification is accepted with the Australian standard AS60079 conforming with its equivalent IEC60079 to comply.
When choosing a product that has IECEx certification, the organisation doesn’t incur testing and certifying costs, the product can go straight into the organisation and can be used internationally.
IECEx certification includes the equipment and installation, manufacture, operation and maintenance of products.
Since its inception in 1996, IECEx has increased from less than 12 member countries to 33 countries. IECEx began certifying only Ex electrical equipment but has since grown to include non-electrical (mechanical) equipment. IECEx has successfully facilitated international trade in equipment and services in explosive environments. IECEx continually reviews and improves by inputting new technologies, new ideas and accidents that have occurred as a result of unforeseen risks.
Certified products bear the blue and white logo.
ATEX vs IECEx
All equipment that meets either ATEX or IECEx certifications have met strict requirements and have been thoroughly tested to work safely in explosive environments.
The main difference between ATEX and IECEx is the countries that accept the certification. IEXEx certification is more widely recognised and accepted around the world than ATEX, with Australian organisations recognising IECEx certification, but not ATEX.
Conformity Assessment Document (CAD)
If a worksite has equipment with no IECEx certification, a Conformity Assessment Document is required by law. All electrical equipment used in a hazardous area must comply with the conformity assessment.
If you have further questions about ATEX and IECEx certifications within Australia, chat with our team by calling 1300 131 933, or get in touch with us online.